What Is Tamper Evident Adhesive Tape?
Tamper Evident Adhesive Tape is a specialized security packaging solution designed to show visible signs when a package has been opened or interfered with, ensuring the integrity of the package using Tamper Evident Adhesive Tape.
Unlike traditional tape, tamper evident tape includes built-in features such as VOID messages or residue markings that instantly alert handlers and recipients to unauthorized access.
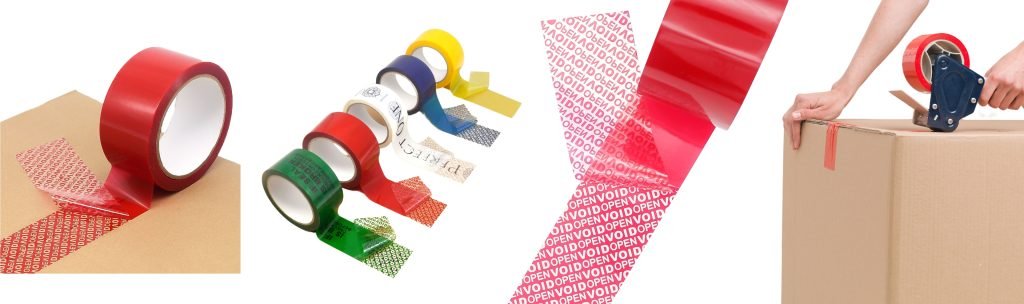
This makes Tamper Evident Adhesive Tape ideal for protecting sensitive shipments in industries such as healthcare, logistics, banking, and electronics, where the use of Tamper Evident Adhesive Tape is crucial for security.
With rising demand for product integrity and regulatory compliance, understanding the different adhesive types used in Tamper Evident Adhesive Tape is critical for choosing the right product.
Water-Based Adhesive Tape: Eco-Friendly and Cost-Effective
Water-based tamper evident adhesive tape is manufactured using water as the primary carrier or solvent for its adhesive formulation. This makes it one of the most environmentally friendly options available in the security packaging industry. Unlike solvent-based alternatives that may emit volatile organic compounds (VOCs), water-based adhesives are non-toxic, have low VOC emissions, and are safer for both users and the environment.
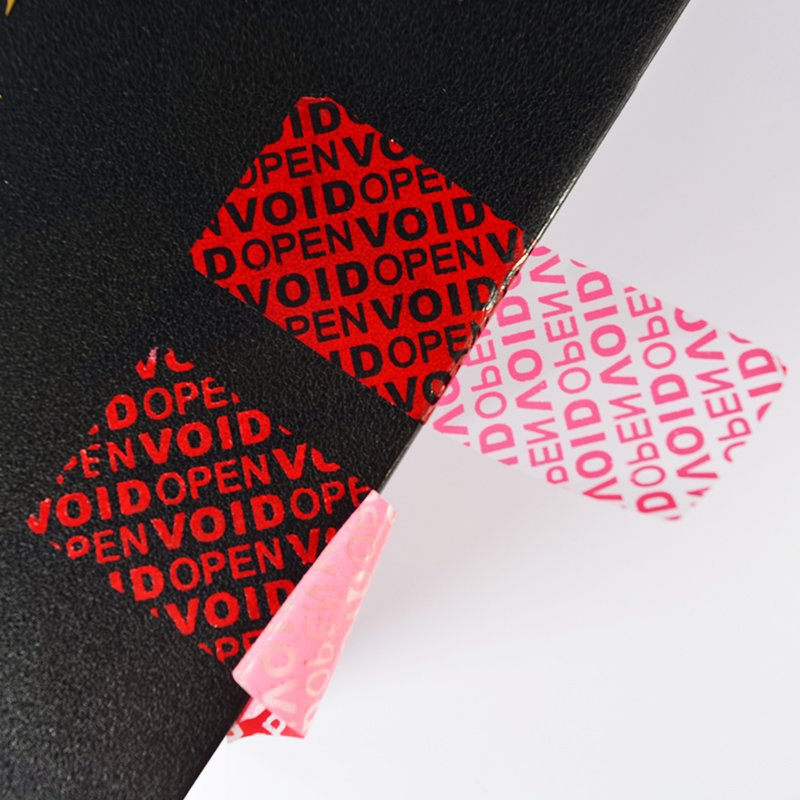
These tapes are ideal for brands that prioritize sustainability without compromising basic security needs. Their adhesion strength is moderate—strong enough to seal packages effectively but gentle enough for materials like cardboard and kraft paper. Because of this, they are widely used in scenarios where package integrity is important but the risk of tampering is relatively low to moderate.
Key Benefits:
- Eco-Friendly Composition: The adhesive is made with water as a solvent, resulting in low environmental impact and safe handling.
- Non-Toxic and Low VOC Emissions: Ideal for businesses seeking sustainable packaging solutions that meet green certification requirements.
- Easy to Recycle: These tapes are often compatible with paper-based recycling streams, supporting closed-loop packaging systems.
- Residue-Free Removal: While providing tamper-evident functionality, they can often be removed without leaving sticky residue, which simplifies package reuse or inspection.
Typical Use Cases:
- E-Commerce Shipments: Ideal for lightweight goods such as apparel, accessories, or printed materials where excessive tamper protection is unnecessary.
- Retail Packaging: Especially for brands using kraft paper boxes or biodegradable mailers.
- Sustainability-Focused Brands: Companies promoting low-waste operations and reduced carbon emissions prefer water-based tamper evident adhesive tape for brand alignment.
- General-Purpose Shipping: Suitable for warehouse operations or fulfillment centers that want consistent, affordable security tape for daily dispatches.
Overall, water-based tamper evident adhesive tape strikes an effective balance between basic tamper resistance and environmental responsibility. For businesses seeking cost-effective packaging with a greener footprint, it offers a compelling solution that aligns with modern consumer values and global sustainability goals.

Oil-Based Adhesive Tape: Long-Lasting Bond Strength
Oil-based tamper evident adhesive tape is engineered with petroleum-derived compounds that offer exceptional bonding strength and durability. These tapes are specifically designed for applications that require strong, lasting adhesion across a wide variety of surfaces, including plastic, metal, and treated paperboard.
Thanks to their robust chemical makeup, oil-based adhesives can withstand challenging environmental conditions such as high humidity, fluctuating temperatures, and chemical exposure. This makes them an excellent choice for industries where packaging needs to remain intact during rough handling, long-distance transportation, or storage in harsh environments.
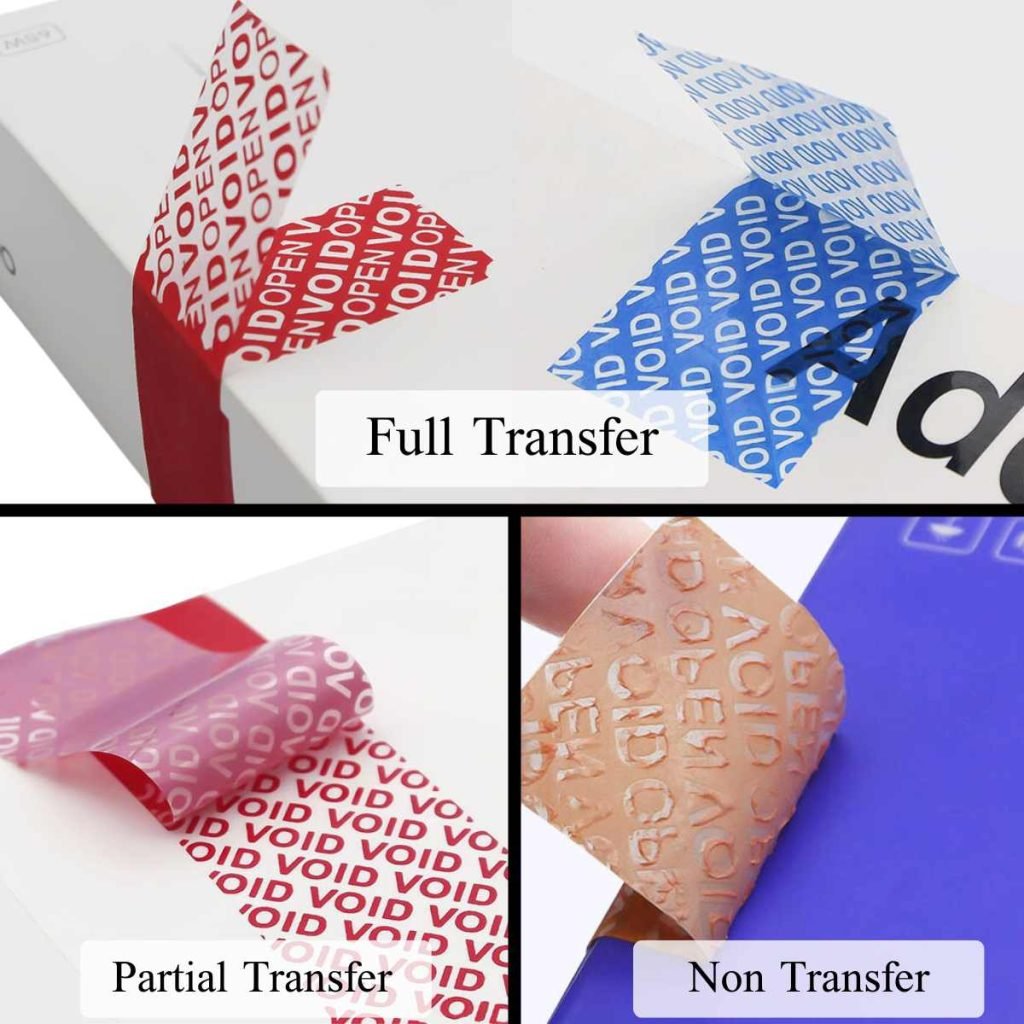
Key Benefits:
- Exceptional Adhesion Power: Provides a strong and secure seal that resists peeling, lifting, or accidental opening—ideal for high-security needs.
- Resistant to Harsh Conditions: Performs reliably in environments with moisture, high heat, and exposure to oils or solvents.
- Versatile Surface Compatibility: Adheres well to non-porous materials such as plastics, aluminum, and poly bags, making it suitable for industrial use.
- Enhanced Tamper Protection: Designed to visibly show signs of tampering such as residue, tearing, or label distortion, offering an extra layer of security assurance.
Typical Use Cases:
- Industrial Packaging: Used in sealing machinery parts, automotive components, and construction materials that require tamper-evident protection during shipment or warehousing.
- Electronics and Precision Equipment: Often applied to secure packaging for circuit boards, cables, and sensitive instruments, ensuring they arrive in pristine condition.
- Plastic and Metal Containers: Perfect for sealing drums, containers, and bottles where strong adhesion is required to resist leakage or unauthorized opening.
- Export and High-Risk Transit Routes: Ideal for international shipping or high-value cargo that demands additional layers of security due to prolonged transit times and multiple handling stages.
Overall, oil-based tamper evident adhesive tape is the preferred choice for businesses needing superior durability and protection against environmental stressors. Its ability to maintain a tight seal in extreme conditions makes it essential for packaging applications where failure is not an option and security is paramount.
Hot Melt Security Tape: Fast, Efficient, and Reliable
Hot melt tamper evident adhesive tape is manufactured using thermoplastic polymers that are melted, applied, and then rapidly cooled to form a strong, durable bond. This tape technology is favored for its instant adhesion, fast-setting properties, and adaptability to automated packaging environments. When speed, reliability, and tamper resistance are critical, hot melt adhesives deliver an optimal solution.
Hot melt adhesive formulas are designed to bond quickly upon application, creating a secure seal without the need for curing or drying time. This makes them highly suitable for high-speed production lines where efficiency is paramount. In addition to speed, hot melt tapes provide excellent shear resistance and hold up well on surfaces that are textured, dusty, or uneven, where other adhesives might struggle.
Key Benefits:
- Rapid Bonding Performance: Offers near-instant adhesion, reducing packaging time and increasing throughput on high-speed automated systems.
- Reliable Tamper Evidence: Once applied, the tape forms a permanent bond that reveals clear signs of tampering, such as tearing, stretching, or surface damage.
- Excellent Shear and Peel Strength: Maintains a secure hold even under stress or shifting loads during transit.
- Surface Flexibility: Works effectively on a wide range of surfaces, including corrugated cardboard, kraft paper, and certain plastic films, making it ideal for mixed material packaging.
- Temperature Resilience: Performs well across a moderate temperature range, suitable for warehouse environments and short-term outdoor exposure.
Typical Use Cases:
- E-commerce Fulfillment Centers: Used extensively in operations where thousands of packages are sealed daily. The speed of hot melt tape streamlines packing while ensuring packages remain secure until they reach the customer.
- Retail and Consumer Goods Packaging: Ideal for sealing branded boxes, electronics, or high-theft-risk items that require both visual deterrence and brand consistency.
- High-Volume Shipping & Logistics: Hot melt tamper evident adhesive tape is commonly deployed in third-party logistics (3PL) facilities, distribution centers, and courier networks where efficiency and tamper control are key.
- Subscription Box Services: Businesses offering monthly product deliveries benefit from the professional appearance, quick application, and security assurances hot melt tape provides.
In summary, hot melt tamper evident adhesive tape delivers a powerful combination of speed, adhesion strength, and tamper detection. It’s a preferred choice for businesses focused on scalability and operational efficiency, while maintaining a high standard of product security throughout the shipping process.
Comparison Table: Which Adhesive Is Right for You?
Feature | Water-Based | Oil-Based | Hot Melt |
---|---|---|---|
Adhesion Strength | Moderate | Strong | Strong |
Eco-Friendly | Yes | No | Partial |
Residue Type | Light | Heavy | Medium |
Ideal Applications | Cartons, Paper | Plastic, Metal | Bulk Shipments |
Cost Efficiency | High | Medium | High |
Application Tips and Industry Use Cases
Applying tamper evident adhesive tape correctly is crucial to maximizing its security performance. Each adhesive type—water-based, oil-based, and hot melt—requires specific handling techniques to ensure tamper evidence functions as intended throughout storage, transit, and delivery.
Water-based tamper evident adhesive tapes should be applied on clean, dry, and smooth surfaces. These tapes perform best in environments with stable humidity and minimal surface contamination. Before application, it’s important to remove dust, grease, or moisture to ensure full contact and effective void message activation upon tampering. Press firmly along the tape’s length to eliminate air bubbles and ensure edge-to-edge adhesion.
Oil-based tamper evident adhesive tapes are ideal for challenging environments. Their robust adhesion makes them suitable for surfaces exposed to moisture, oil, or temperature fluctuations. Apply with firm pressure to irregular surfaces like plastic containers, glossy finishes, or coated metal. For best results, use a hand roller or automated pressure device to ensure consistent contact across the tape’s width.
Hot melt tamper evident adhesive tapes are preferred in high-speed, automated packing systems. To maximize performance, these tapes should be applied using temperature-controlled dispensers, ensuring the adhesive remains tacky during placement. Once cooled, they form a secure bond resistant to shear, peel, or lifting. Regular maintenance of dispensers and temperature calibration is recommended to maintain consistent quality.
Industries That Benefit from Tamper Evident Adhesive Tape
Tamper evident adhesive tape is widely used across a range of industries where product integrity, regulatory compliance, and customer trust are critical:
- Pharmaceutical Distribution: These tapes are used to seal medicine cartons, prescription shipments, and medical kits. In this industry, tamper evidence is essential for meeting regulations like the U.S. FDA’s guidelines on tamper-resistant packaging and the EU Falsified Medicines Directive.
- Government and Legal Document Transport: When handling confidential records, legal documents, or ballot boxes, tamper evident adhesive tape ensures that contents have not been accessed or altered during transit. Security bags sealed with these tapes offer visible proof of integrity for high-stakes materials.
- High-End Consumer Electronics: Electronics such as smartphones, gaming consoles, and accessories are often targeted for theft or tampering. Using branded, tamper evident adhesive tape reinforces a secure, professional packaging appearance while protecting product value and warranty claims.
- E-Commerce and Fulfillment Platforms: Online retailers and third-party logistics (3PL) centers rely on hot melt or water-based tamper tapes to ensure packages are sealed securely before delivery. This adds a layer of security that reduces disputes, fraud claims, and customer dissatisfaction due to tampering.
- Luxury Goods and Specialty Packaging: In sectors like cosmetics, perfumes, or high-value retail, tamper evident tape serves both security and branding functions. Custom-printed tapes with logos or security text demonstrate a commitment to product authenticity.
In all of these industries, tamper evident adhesive tape not only helps prevent unauthorized access but also plays a critical role in reinforcing brand integrity, achieving compliance with international safety standards, and enhancing customer confidence in the delivered product.
Conclusion: Choosing the Best Tamper Evident Adhesive Tape
Selecting the best tamper evident adhesive tape is a critical decision for any business concerned with product integrity, customer trust, and regulatory compliance. The right choice depends on several factors, including your packaging materials, shipping conditions, industry-specific requirements, and long-term sustainability goals.
For businesses prioritizing eco-friendliness, water-based tamper evident adhesive tape offers a low-VOC, biodegradable option that aligns with green packaging initiatives. These tapes are ideal for e-commerce, lightweight parcels, and brands focused on minimizing their environmental footprint.
If your products require superior durability under challenging conditions such as high humidity, exposure to chemicals, or temperature variations, oil-based tamper evident adhesive tape provides a robust and reliable bond. It’s commonly used in industrial packaging, electronics, and manufacturing applications where tape failure is not an option.
On the other hand, companies with high-volume operations or automated packing lines may benefit from hot melt tamper evident adhesive tape, known for its quick tack, efficiency, and compatibility with fast-paced environments. These tapes are widely adopted in fulfillment centers and retail packaging operations due to their speed and consistency.
Each adhesive type comes with its own set of benefits, and understanding these differences can help your team implement a more secure, efficient, and cost-effective packaging solution.
At EcoSecurity Tape, we offer a full range of customizable tamper evident adhesive tapes designed to meet specific security challenges. Contact us today to learn more or request free samples tailored to your business needs.
Our commitment to quality, compliance, and innovation ensures that your shipments are protected from unauthorized access—safeguarding not only your products but also your brand reputation.
📦 Ready to get started? Contact us today to learn more about our tamper evident adhesive tape solutions, request a quote, or receive free sample packs customized for your industry. We’re here to help you build smarter, safer packaging strategies.