Adhesive tape manufacturing plays a critical role across industries such as packaging, electronics, automotive, and healthcare.
Whether you’re producing pressure-sensitive security tape or customizing tamper-evident rolls, mastering the tape production process is essential for ensuring quality, efficiency, and product integrity.
In modern adhesive tape production, manufacturers focus not only on material performance but also on environmental responsibility. The selection of eco-friendly substrates, solvent-free adhesives, and energy-efficient processes helps companies meet sustainability goals while reducing operational costs.
Automation is another key driver in today’s adhesive tape manufacturing environment. From automated film blowing lines to precision slitting machines, investing in advanced technology ensures consistent thickness, strong adhesion, and reduced defect rates—critical factors for industries where performance and safety cannot be compromised.
Furthermore, integrating ISO-certified quality management systems strengthens customer confidence and compliance with international standards. Periodic batch testing for tensile strength, peel adhesion, and temperature resistance ensures every roll meets or exceeds specifications.
Global competition also means that manufacturers must adapt quickly to changing market needs. This includes offering small-batch customization, rapid prototyping, and just-in-time delivery to support B2B clients in sectors like logistics, pharmaceuticals, and high-tech manufacturing.
By combining cutting-edge technology, skilled workforce training, and rigorous quality control, companies can position themselves as trusted leaders in the adhesive tape production industry.
Introduction
Understanding the evolution and application of adhesive tape is essential for mastering modern adhesive tape production tips. Since the invention of the first adhesive tape in 1925, these products have become indispensable across countless industries—gradually replacing traditional fasteners like screws and welding.
This shift not only simplified manufacturing but also improved efficiency, surface protection, and material compatibility across numerous applications.
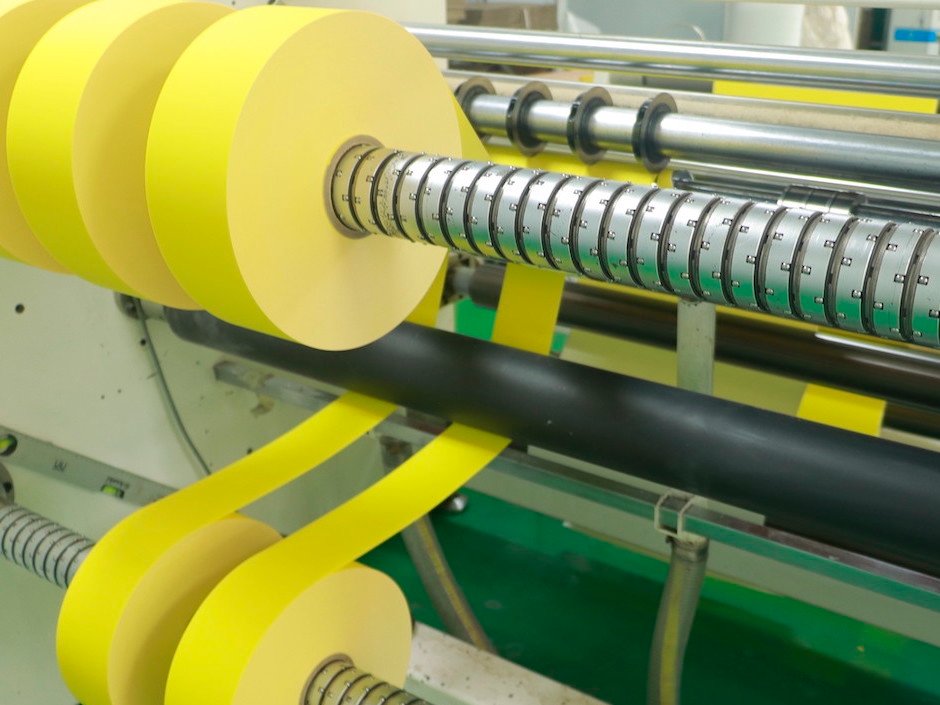
Importance of Adhesive Tapes in Modern Industries
- Process Simplification: Adhesive tapes streamline assembly lines by providing quick, clean, and reliable bonding solutions.
- Surface Protection: They minimize damage during handling and transport, particularly in sectors like automotive, electronics, and aerospace.
Brief History and Evolution
- 1925: Introduction of the first commercial adhesive tape.
- Technological Advancements: Emergence of water-activated, heat-activated, and pressure-sensitive adhesives (PSA).
- Modern Applications: Extensively used in packaging, healthcare, electronics, and aerospace.
As you explore practical adhesive tape production tips, understanding this history and versatility highlights why adhesive tapes are not only foundational in industrial processes but also a driver of innovation in specialized applications.
Types of Adhesive Tapes
One of the most fundamental adhesive tape production tips is understanding the distinct types of tapes available. Each category offers specific performance characteristics suited to different industries and application scenarios. Choosing the right type is essential for ensuring bonding effectiveness, cost-efficiency, and product longevity.
Water-Activated Tape
- Characteristics: Activated by water to create a strong bond with corrugated surfaces.
- Common Uses: Sealing cartons, e-commerce packaging, export logistics.
- Advantages: Tamper-evident, eco-friendly, recyclable.
- Disadvantages: Requires water dispenser; limited adhesion to glossy or non-porous surfaces.
Heat-Activated Tape
- Characteristics: Requires elevated temperatures to bond securely.
- Common Uses: Automotive assembly, insulation, industrial bonding.
- Advantages: Exceptional durability and strength once activated.
- Disadvantages: Longer application time; requires heating equipment.
Pressure-Sensitive Adhesive (PSA) Tapes
- Characteristics: Bonds instantly under light pressure, no heat or solvent required.
- Common Uses: Medical device assembly, electronics, consumer packaging.
- Advantages: Easy to apply, versatile, compatible with automated lines.
- Disadvantages: May lose performance in high-temperature or high-moisture environments.
One of the key adhesive tape production tips for manufacturers is aligning the tape type with the application’s environmental conditions, material compatibility, and performance expectations. Selecting the wrong adhesive base or activation method can lead to product failure or reduced shelf life.
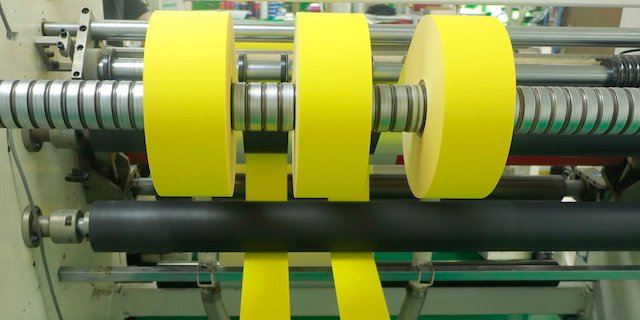
Key Components in Adhesive Tape Production
One of the most important adhesive tape production tips is understanding the materials that define tape performance. High-quality adhesive tapes are the result of carefully selected base layers and specialized adhesives tailored for specific uses and environments.
Backing Materials
The backbone of any adhesive tape is its backing material, which determines flexibility, tensile strength, and durability. Common types include:
- Polypropylene Film: Durable and moisture-resistant, widely used in packaging tapes.
- Paper: Lightweight and flexible, ideal for masking and eco-friendly applications.
- Cloth: High tensile strength; commonly used in duct and industrial-grade tapes.
- Foam: Provides cushioning and gap-filling, used in mounting or insulation applications.
- Metal Foil: Heat- and electricity-conductive, suitable for HVAC and shielding purposes.
Adhesive Types
Choosing the right adhesive is another essential area in adhesive tape production tips, as it directly affects adhesion strength, environmental resistance, and application compatibility.
- Rubber-Based Adhesives:
- Natural Rubber: Excellent tack and performance on rough surfaces.
- Synthetic Rubber: Better temperature and aging resistance.
- Acrylic Adhesives:
Highly stable against UV light and oxidation, ideal for outdoor and long-term applications. Offers balanced adhesion and transparency. - Silicone Adhesives:
Performs well in extreme temperatures and adheres to low-surface-energy materials. Commonly used in medical and high-performance industrial settings.
Selecting the optimal combination of backing material and adhesive type is a cornerstone of effective adhesive tape production tips. This alignment ensures the tape meets functional and regulatory standards for its intended use.
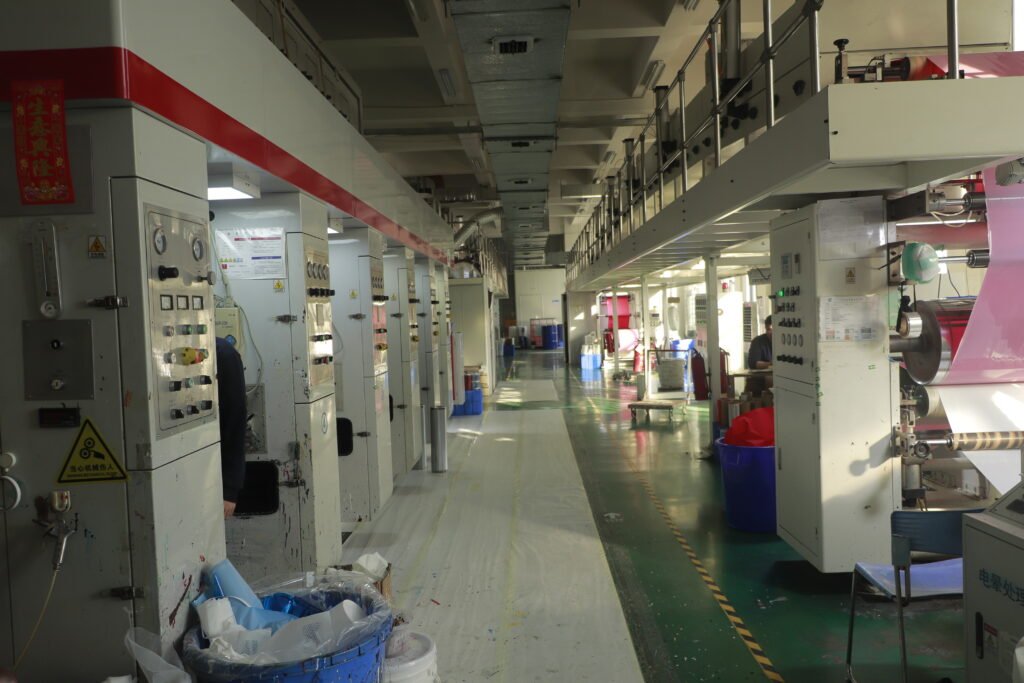
✅ For more on ensuring tape reliability and compliance, see our Quality Guarantee.
By mastering these material choices, manufacturers can improve consistency, reduce defects, and enhance tape performance across diverse industries.
The Adhesive Tape Manufacturing Process
Mastering each step in the production line is central to effective adhesive tape production tips. From raw material conversion to final roll finishing, this process shapes the performance, durability, and value of every industrial roll.
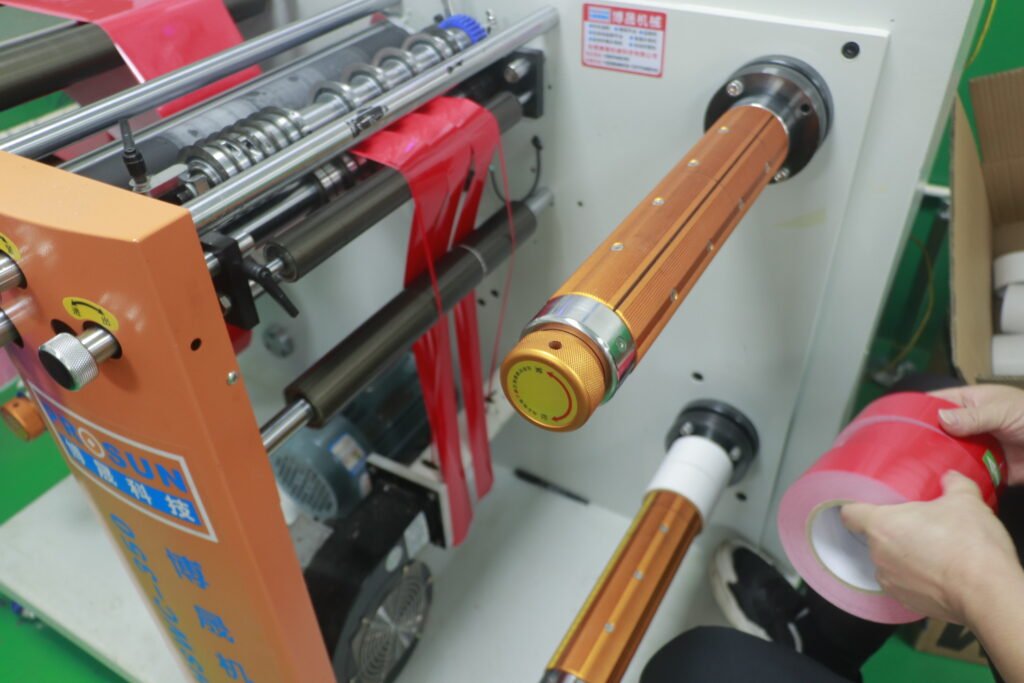
1. Film Blowing: Creating the Backing Material
The film blowing stage is foundational in industrial tape manufacturing, as it produces the flexible backing that supports the adhesive layer. The process begins with polymerizing raw materials—commonly polypropylene—into long-chain polymers. The molten polymer is then extruded through a circular die and inflated to achieve the desired thickness and width.
Advantages:
- Produces consistent and uniform film
- Supports custom dimensions for custom adhesive tape manufacturing
- Efficient use of polymers and additives
Disadvantages:
- Requires advanced machinery
- Sensitive to temperature and humidity changes
Once cooled and flattened, the film is rolled and prepared for adhesive application. This precise control ensures the mechanical strength needed for sectors like pressure-sensitive tape production and medical-grade films.
📌 For those exploring security packaging, see our tamper-proof label solutions and guide on evaluating tamper-evident tapes.
2. Gluing: Applying the Adhesive Layer with Precision
The adhesive coating step is a pivotal part of all adhesive tape production tips, directly affecting tack, peel strength, and shelf stability. Using roll, slot die, or extrusion methods, adhesives are applied to the backing material in a controlled environment.
Key Actions:
- Selection of rubber, acrylic, or silicone adhesives based on end use
- Fine-tuning coating thickness to match tolerance specs
- Inline adhesive tape quality control for consistency and defect prevention
This step is especially critical for pressure-sensitive tape production, where uniform adhesive distribution impacts performance across high-speed applications like electronics and consumer packaging.
3. Drying and Rewinding: Setting Adhesive Integrity
Post-application, the tape passes through temperature-controlled drying chambers. Whether using heat or UV, this process cures the adhesive and eliminates any residual solvents or moisture.
Why It Matters:
- Prevents adhesive delamination or failure under stress
- Maintains adhesion strength during long-term storage
- Prepares rolls for precision rewinding with consistent tension
Rewinding ensures roll integrity, reduces slack or air bubbles, and prepares tapes for final slitting. In custom adhesive tape manufacturing, this step supports exact core sizes and batch labeling for traceability.
4. Slitting: Converting Rolls for Market Use
The final major phase of industrial tape manufacturing is slitting—cutting wide master rolls into usable formats based on application demand.
Key Considerations:
- High-precision rotary or razor slitting ensures clean, burr-free edges
- Custom widths serve diverse sectors—from narrow surgical tape to wide carton sealing tape
- Real-time adhesive tape quality control checks dimensional consistency and edge finish
For clients in custom adhesive tape manufacturing, this stage allows high SKU flexibility, private-label branding, and efficient bulk packaging.
Quality Control Measures in Adhesive Tape Manufacturing
One of the most critical adhesive tape production tips is maintaining rigorous quality control at every stage of the manufacturing process. Whether you’re engaged in industrial tape manufacturing or custom adhesive tape manufacturing, consistent product performance depends on well-defined inspection and testing protocols.
Key Quality Control Steps
Implementing effective quality assurance is one of the most critical adhesive tape production tips, especially for manufacturers involved in pressure-sensitive tape production and other high-performance applications. Below are essential QC steps widely used in industrial tape manufacturing today:
Raw Material Inspection
Quality begins at the source. Backing materials such as polypropylene film and adhesives are tested for purity, tensile strength, and compatibility. Poor input materials often result in failures later in custom adhesive tape manufacturing. ASTM standards like ASTM D3330 provide guidance for peel adhesion testing in tapes and pressure-sensitive products.
In-Process Monitoring
Throughout production, inline monitoring systems track variables such as coating thickness, roll width, adhesive distribution, and curing temperature. These checks ensure that deviations are corrected before reaching final stages, reinforcing consistent adhesive tape quality control.
Adhesion Testing
Standardized methods, including peel, shear, and tack testing, simulate real-world stress. These tests ensure bond strength under various applications—especially important in aerospace, automotive, or medical-grade tapes.
Environmental Stability Tests
Tapes undergo rigorous exposure to temperature, moisture, and UV cycles to assess long-term durability. For sectors such as healthcare or food packaging, resilience against environmental stress is non-negotiable.
Final Product Inspection
Every finished roll is reviewed for dimensional accuracy, clean slitting, visual integrity, and core alignment. This stage ensures compliance with specifications before entering distribution.
✅ Learn more about standardized testing protocols at ASTM.org, which governs many adhesive tape quality benchmarks worldwide.
By implementing these quality protocols, manufacturers not only meet industry compliance standards but also enhance brand credibility. For companies pursuing custom adhesive tape manufacturing, consistent QC builds trust with private-label clients and end users alike.
✅ Pro Tip: Integrate automated vision systems and digital QC logs to improve efficiency and traceability in your adhesive tape production line.
Applications Across Industries
A key aspect of applying adhesive tape production tips effectively is understanding how different types of tapes meet the specific demands of various industries. From life-saving medical applications to aerospace-grade engineering and high-volume packaging lines, the role of adhesive tape continues to expand alongside innovations in industrial tape manufacturing.
1. Medical Industry Applications: Enhancing Patient Care with Specialized Tapes
In the medical sector, adhesive tapes play an integral role in improving patient outcomes and enabling efficient care delivery. Manufacturers involved in custom adhesive tape manufacturing must ensure their products are hypoallergenic, biocompatible, and sterile.
Key Applications:
- Surgical Tape: Secures dressings and medical devices with minimal skin trauma.
- Patient Monitoring: Holds IV lines, catheters, and ECG leads; requires skin-safe adhesives.
- Wound Care: Creates a sterile seal to protect against infection and accelerate healing.
In this industry, adhesive tape quality control is critical, as the reliability of tape adhesion directly affects patient safety and clinical performance.
2. Aerospace Industry Applications: Lightweight Solutions for Structural Integrity
In aerospace, where weight reduction and environmental resistance are mission-critical, pressure-sensitive tape production offers innovative alternatives to mechanical fasteners.
Key Applications:
- Component Bonding & Sealing: Replaces rivets and screws, reducing aircraft weight.
- Thermal & Electrical Insulation: Protects sensitive avionics from temperature extremes.
- Corrosion Resistance: Specialized tapes prolong equipment lifespan in harsh conditions.
Because of the high stakes involved, manufacturers prioritize precision adhesive tape production tips, ensuring that tapes meet aviation-grade standards through advanced industrial tape manufacturing methods.
3. Packaging Industry Applications: Ensuring Food Safety and Shipping Efficiency
Packaging is one of the most dynamic areas of adhesive tape production, where large-scale manufacturing meets strict quality demands and consumer-facing aesthetics.
Key Applications:
- Carton Sealing: Pressure-sensitive adhesive tapes are widely used to secure packages and deter tampering.
- Temperature-Safe Tapes: Ideal for frozen foods or temperature-sensitive logistics.
- Printed & Tamper-Evident Tapes: Enable brand visibility and consumer trust.
In this sector, applying adhesive tape quality control practices is essential to ensure consistency across high-speed lines and maintain brand integrity. Businesses that leverage custom adhesive tape manufacturing can tailor packaging tapes to different substrates, from cardboard to plastic.
By exploring these industry-specific use cases, manufacturers can apply targeted adhesive tape production tips to improve efficiency, meet regulatory demands, and offer competitive, application-ready solutions.
Expert Insights on Manufacturing Best Practices in Adhesive Tape Production
Industry experts emphasize theIndustry experts emphasize the importance of precision, consistency, and innovation in Adhesive Tape Production. High-quality manufacturing not only ensures product performance but also builds trust with end users. Below are key best practices adopted by leading adhesive tape manufacturers worldwide:
1. Raw Material Quality
Always source premium-grade raw materials. The consistency of both backing and adhesive components directly affects durability, tackiness, and temperature resistance.
For example, selecting PET, BOPP, or PVC films with uniform thickness and adhesives with stable viscosity can significantly improve adhesive tape production output.
2. Advanced Technology
Utilize cutting-edge machinery for film blowing, coating, lamination, and slitting. Automated lines with precision control systems ensure uniform coating thickness and reduce the likelihood of defects. Incorporating smart manufacturing technologies—such as IoT sensors—can further optimize adhesive tape production processes.
3. Regular Maintenance
Maintain all equipment on a strict schedule to avoid unexpected breakdowns. Well-maintained coating and slitting machines improve operational efficiency and reduce scrap rates, lowering the overall cost of adhesive tape production.
4. Quality Control
Implement multi-stage quality control checks:
- Incoming materials inspection to verify film, liner, and adhesive consistency
- In-process monitoring for coating accuracy and curing quality
- Post-production testing for adhesion strength, peel resistance, and temperature endurance
Advanced optical inspection systems and tensile testing machines can help ensure the highest product standards.
5. Employee Training
Invest in continuous training programs for operators, engineers, and QC teams. Skilled staff are better equipped to spot production anomalies early, minimize wastage, and adapt to new adhesive tape production technologies.
6. Environmental Compliance & Sustainability
Modern adhesive tape production facilities are increasingly adopting eco-friendly processes. This includes:
- Using water-based adhesives to reduce VOC emissions
- Recycling production waste
- Sourcing biodegradable or recyclable backings
These measures not only reduce environmental impact but also appeal to eco-conscious clients.
7. Customization Capabilities
In competitive markets, offering custom widths, colors, prints, and security features—such as tamper-evident patterns or holograms—can significantly differentiate your adhesive tape products. Customization requires flexible manufacturing lines and close collaboration with clients during the design phase.
✅ Adhering to these best practices in adhesive tape production not only enhances product performance but also strengthens your brand’s reputation, increases market competitiveness, and ensures compliance with international standards.
Need custom adhesive tapes? Let’s manufacture together.
========================================================================